Dow ENDURANCE™ HFDK-4201 SC
DOW ENDURANCE™ HFDK-4201 SC is recommended for the insulation of high voltage power transmission cables rated up to 230 kV.
Specifications
HFDK-4201 SC is designed for use in power distribution and transmission cables. Cables insulated with HFDK-4201 SC, using sound commercial manufacturing practice, would be expected to meet the latest editions of the following specifications and regulations:
- IEC 62067, 60840
- CENELEC HD 632 S3
- GB/T 11017, GB/Z 18890
General Properties
Access the complete datasheet details for Dow ENDURANCE™ HFDK-4201 SC when you create your free account with Prospector. You’ll find complete information on physical, mechanical and hardness specs.
Processing
Find specific processing information for Dow ENDURANCE™ as well as general information for the Polyethylene, Crosslinked generic family. Register or Sign In for more information.
Where To Buy
You can purchase Dow ENDURANCE™ HFDK-4201 SC from 3 distributors or manufacturers. Register or Sign In for more information.
Find UL Yellow Cards
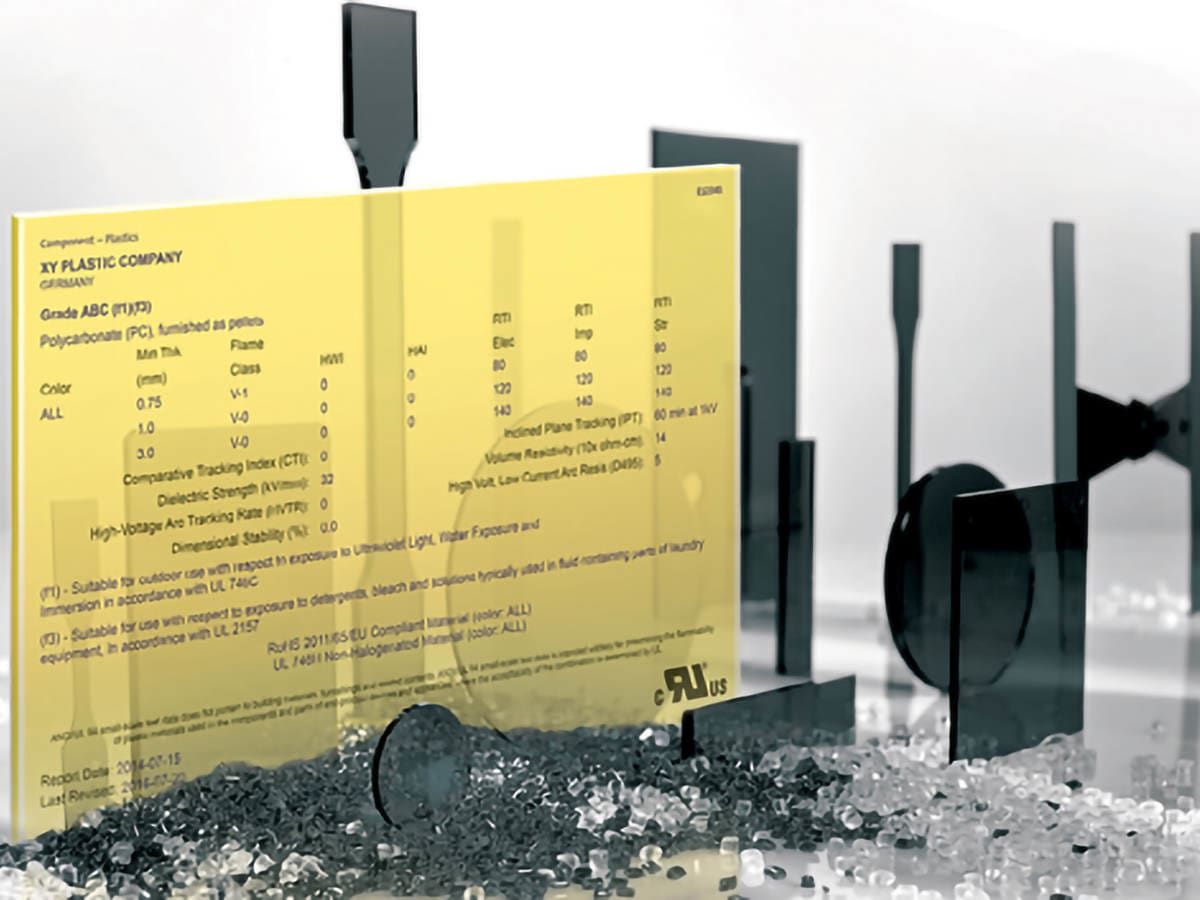
UL's Yellow Cards are a globally recognized safety and quality guarantee, a certified demonstration of how plastics have met a specific set of performance credentials.
PROSPECTOR
Find solutions, not just materials.
When you join Prospector, you leverage the dynamic tools and features to find solutions fast.
Register Today